The temperatures at which food is stored, prepared, or held over are a critical aspect of food safety, but foodservice operators have historically entrusted store employees to manually check temperatures periodically – is the makeline temperature correct, is the refrigerator at 37℉ – and hope that equipment doesn’t stop working while the store is closed.
For restaurants, convenience stores, grocery stores, and other operators dealing with and serving food, this manual approach to temperature monitoring is overly reliant on manual tasks to get it right and introduces too much risk. Today, more operators are automating this process altogether, saving them more money by having less food spoil, improving food safety compliance, and saving their employees time to focus on other important work.
What is automated temperature monitoring?
Automated temperature monitoring automatically checks and reports the temperatures of equipment such as walk-ins, makelines, warmers, coolers, and freezers, and sends alerts to key personnel (managers, maintenance crew, etc.) if temperatures go out of range e.g. a freezer temperature increases by 5°.
How does automated temperature monitoring work?
There are two key components to make automated temperature monitoring work:
- The software and mobile apps that track temperatures, visualize reports, send alerts, etc.
- The hardware, including temperature sensor devices that are placed within your refrigerators or other equipment, gateways that connect the wireless sensors to the internet, and tablets, smartphones or other devices that visualize the data captured from the sensor hardware.
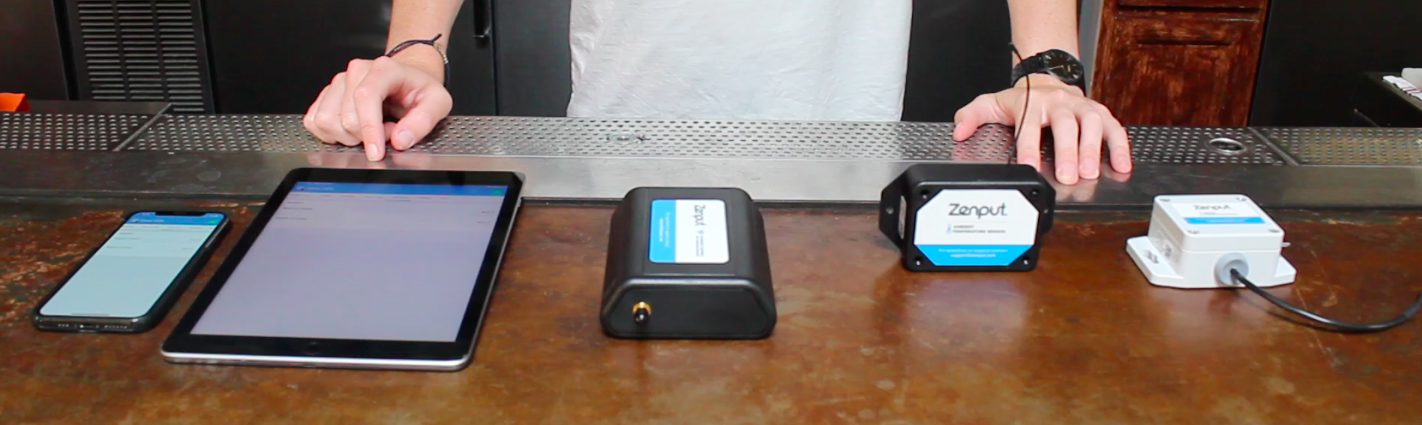
Keeping Track of and Receiving Alerts About Temperatures (Software)
Want to see what temperature your freezer is right now? See reports of temperatures for the last three months? Get an alert if temperatures get too high. This is the software and mobile app side of things.
Here’s how it works with Zenput Temp Monitoring:
Operations leaders, district managers, and others use the Sensor dashboard to view equipment temperatures for every device in every store, They can see the latest temperature reading and a recent trendline to quickly spot any recent discrepancies. By clicking on a single sensor in the dashboard, a detail card reveals the exact time of the last reading, shows whether or not the device is online, and shows a more detailed history of temperatures for the last day, week, month, and year.
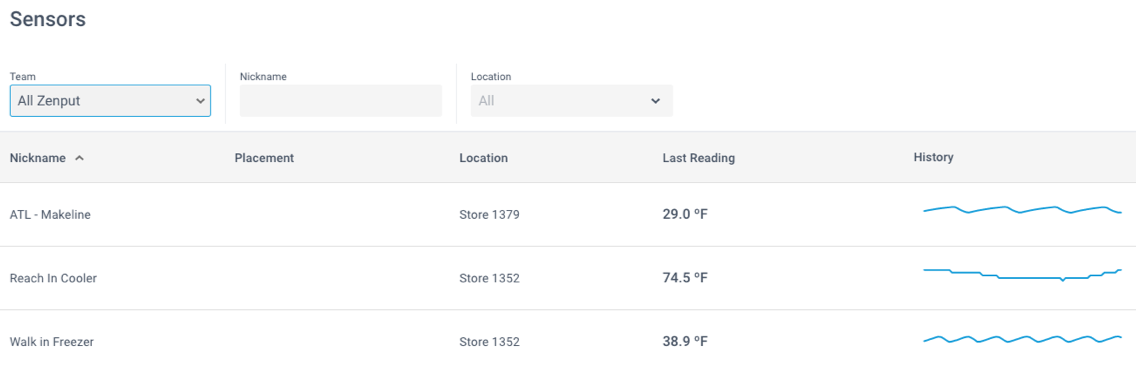
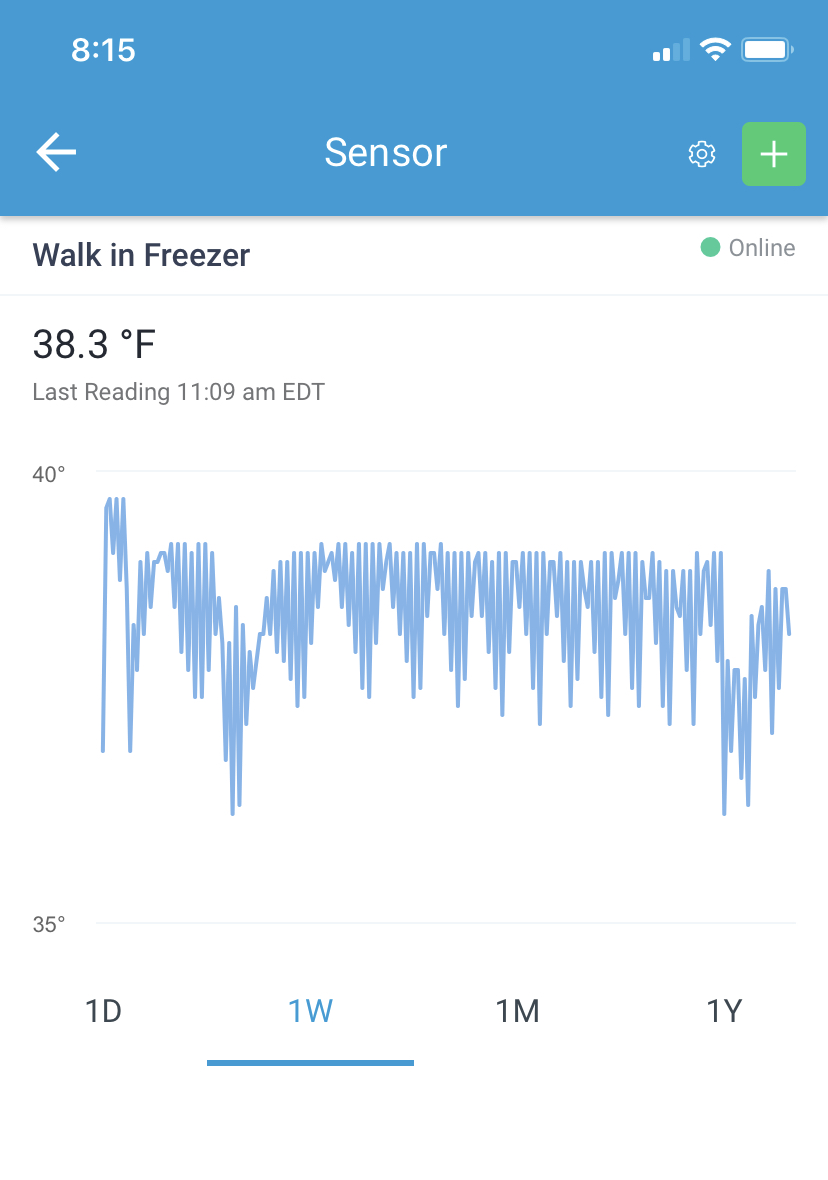
Once a sensor has been placed in a store, you can also create alerts to, for example, send a mobile alert to you, maintenance crew, or others if a sensor temperature goes above 32℉. One Zenput customer shared how this kind of alert saved them more than $5,000 in inventory one night when the freezer shut off unexpectedly at 2am.
In addition to receiving alerts, most of our customers will automatically create a follow-up task for this kind of scenario. This helps hold the store manager or other staff accountable for confirming that the issue has been resolved.
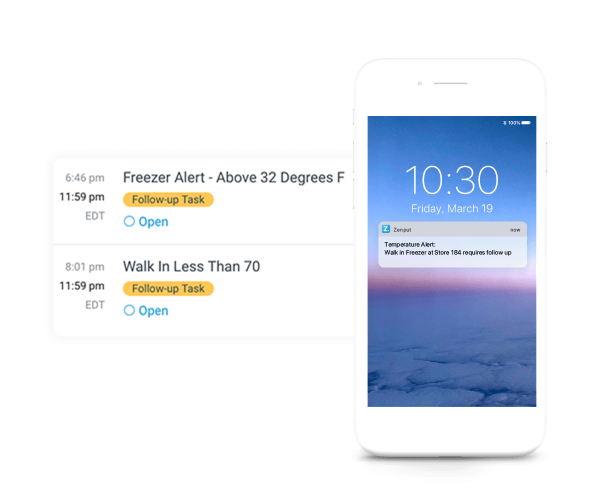
What to Place In Your Stores and Equipment (Hardware)
In order to do the tracking, trending, and alerting that was shared above, physical sensor devices must be placed in your equipment, such as walk-ins, makelines, warmers, coolers, or freezers. Here’s a quick overview of what’s needed to make it all work.
To utilize a temperature monitoring solution like this there are generally three main hardware devices that you’ll need: a gateway, a temperature sensor, and computer or smartphone.
Gateway - Cellular or Ethernet
The gateway for temperature monitoring is like a wireless router that you use for your home or work computer – it connects to the internet and will connect to any/all sensor devices that you set up in a store. You generally only need one of these for a single store location.
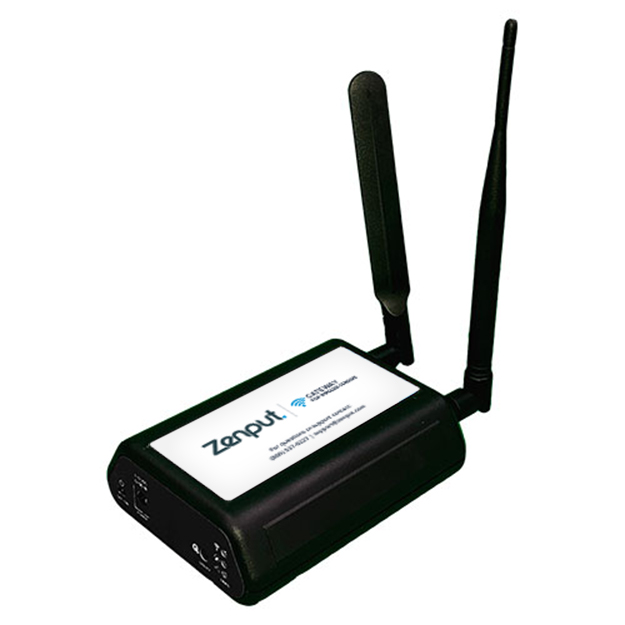
Temperature Sensor
Sensors are what read the actual temperatures of your equipment (e.g. freezer). With Zenput Temp Monitoring, sensors can be screwed into place in your equipment, stick magnetically, etc. and should never be moved from the environment that you place it in.
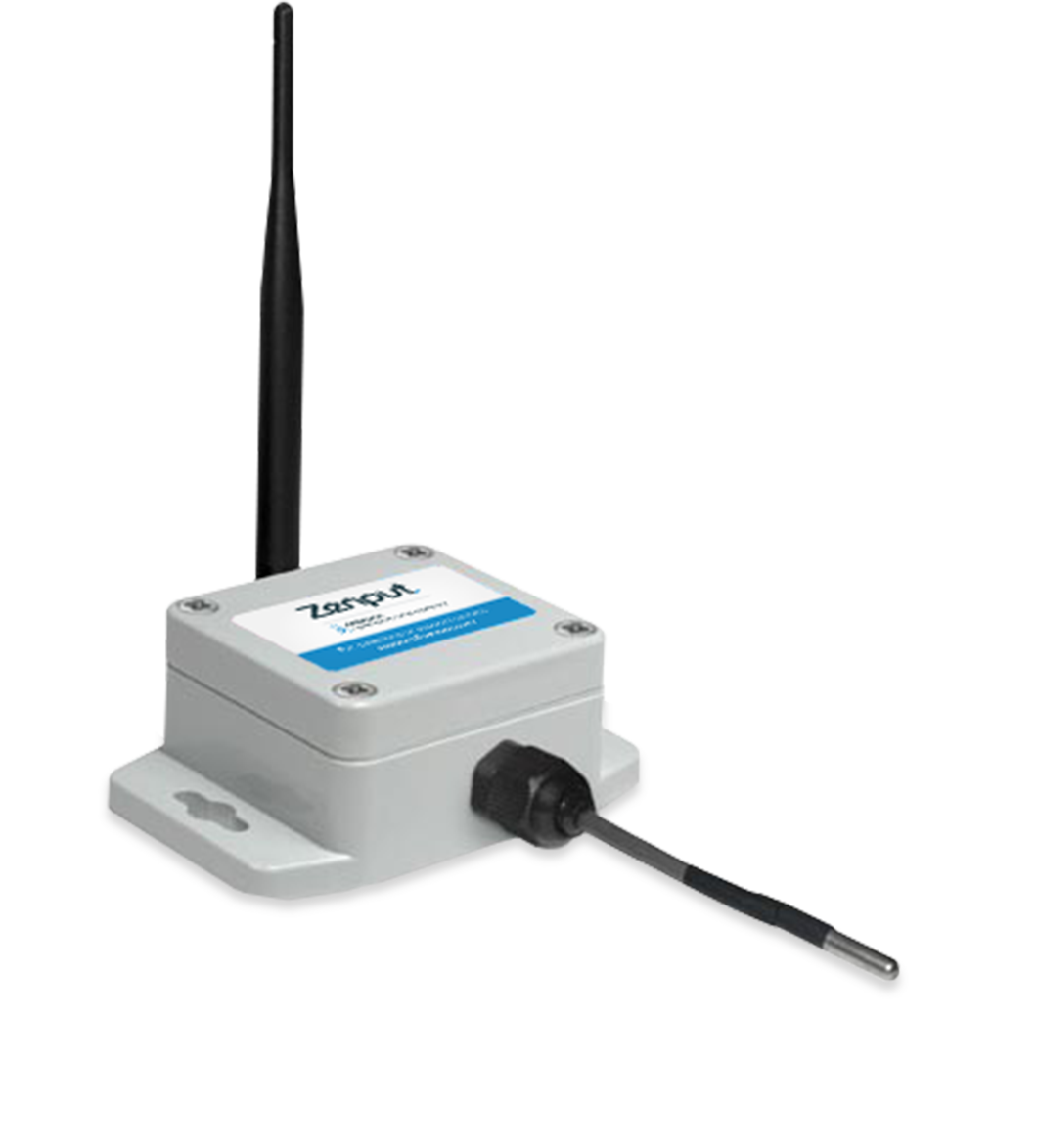
Computer or Smartphone
With Zenput Temp Monitoring, you can use your existing smartphone or computer to access the dashboards that visualize all of this data for you, so you don’t need to buy an additional phone or computer just for your temperature monitoring solution.
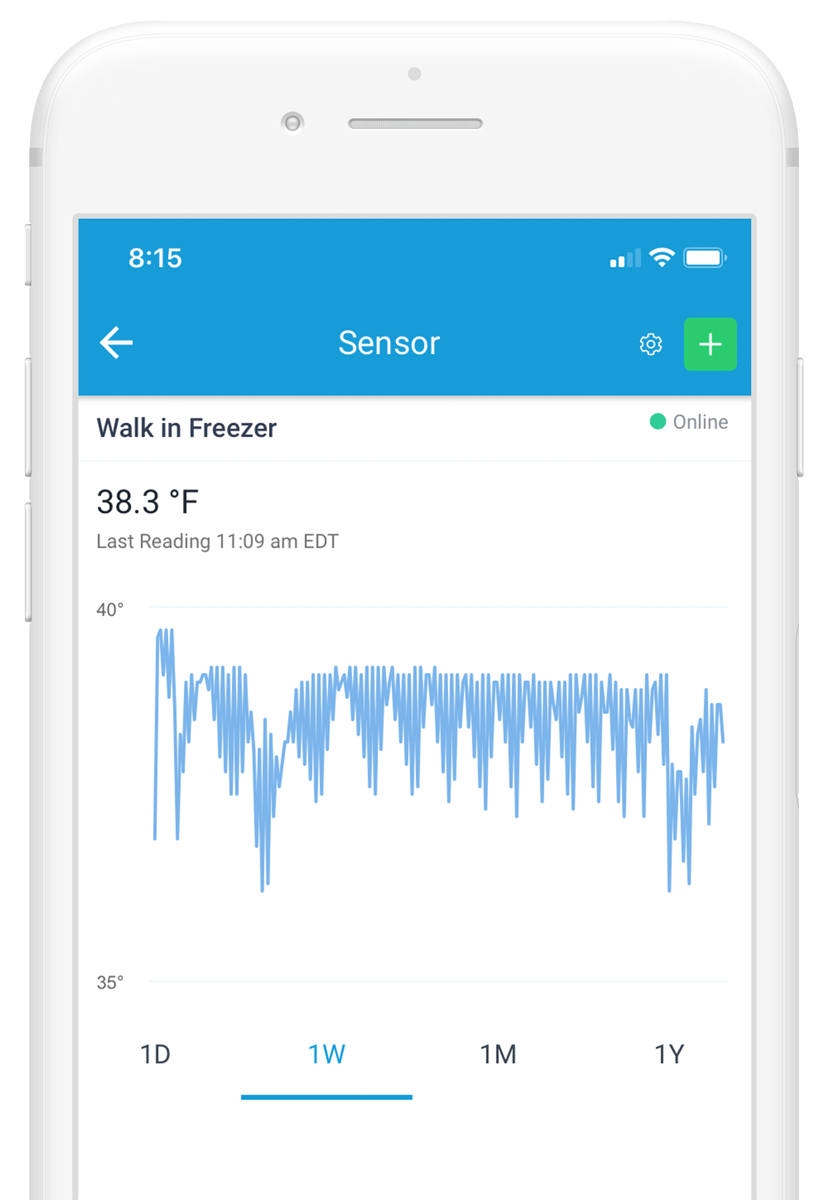
Making the Case for Automated Temperature Monitoring
Any foodservice operator will agree that ensuring food and equipment are at the right temperatures is important, but the reality is that the act of monitoring temperatures today is too manual, too dependent on individuals to spot a high temperature or broken equipment. It leaves too much risk in terms of food safety for customers, liability for the company, and costs associated with losing spoiled inventory.
Especially as field and office staff are spending even less time visiting stores, now is a great opportunity to revisit your approach to temperature monitoring across your operation.
Subscribe to our blog
You are now subscribed!